Optimal Uniform Thickness Deposition with Sybilla Equipment for Enhanced Results
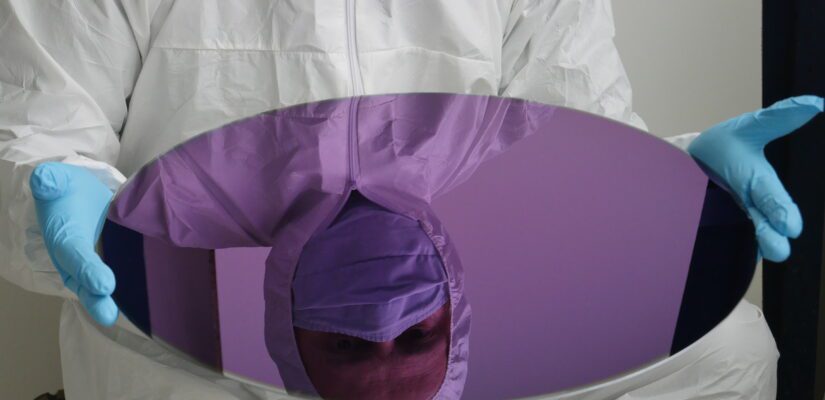
posted Dec 08 2023
Optimal Uniform Thickness Deposition with Sybilla Equipment for Enhanced Results
Embark on a journey into the cutting-edge capabilities of Sybilla equipment, where the realization of optimal uniform deposition thickness is more than just a goal—it’s a reality. Witness the prowess of Sybilla equipment in consistently delivering multi-element thin films on large substrates, reaching up to 450 mm wafers, all without the need for substrate rotation or planetary motion. The commitment to precision uniform deposition is one of the cornerstones of Sybilla’s revolutionary strategy, emphasizing its vital role in the future of oxide thin film materials and architectures.
Optimizing Thin Film Excellence: Sybilla Equipment’s Key Advantages in Uniform Deposition Unveiled
In addition to top quality oxide thin film material properties, Sybilla equipment boasts three key pivotal assets:
- Precision Uniform Deposition: Achieve consistent multi-element (up to 6) thin films on large substrates, demonstrated on up to 450 mm wafers, without the need for substrate rotation or planetary motion. The size of the substrate can be further scaled if needed with same performances.
- Combinatorial Mastery: Leverage a powerful combinatorial facility for:
○ Fast screening and optimization of thin film properties based on chemical composition.
○ Gain in-depth insights into process dynamics and chemical precursor decomposition paths.
- Rapid screening and optimization of device performance using various 3D architectures.Innovative Growth Processes: Experience parallel or serial processes for additive growth, akin to 3D or 4D printing with lateral resolutions between 1 micron to a few millimeters (x, y) and a few nanometers in the growth (z) direction.
Stay tuned for our upcoming blogs, where we will delve into the details, showcasing how Sybilla equipment can efficiently scale R&D results also to production.
Advancing Thin Film Homogeneity further from thickness and encompassing also compositional and crystallographic levels
Achieving uniform thickness, chemical composition, and functional properties in multi-element thin films on larger and larger substrates is a crucial aspect of Sybilla equipment.
The ability to execute uniform thickness deposition on large substrates holds paramount importance, especially when linking thin film thickness to device performances. This uniformity is vital for achieving mass production of identical devices. Thickness homogeneity stands out as the first key performance indicator, easily measured with accuracy and universally applicable across various materials.
While thickness homogeneity is a starting parameter to address device performances, other homogeneity factors such as chemical composition and crystallinity play also essential roles. These parameters serve again as indirect performance indicators, contributing to the comprehensive qualification of a thin film growth equipment.
The ultimate evaluation, however, hinges on the direct measurement of device performance homogeneity, even though it may involve greater complexity and expense. Typically, this comprehensive approach is undertaken in the final stages of equipment development, ensuring the equipment is finely tuned for efficient production.
Optimizing Thin Film Homogeneity: Unveiling Sybilla Equipment’s Exceptional Performances
Experience remarkable thin film homogeneity with Sybilla equipment across various wafer sizes, including 150 mm, 200 mm, 300 mm and 450 mm. Our equipment consistently achieves a homogeneity (peak to peak on the full wafer, excluding a small border for substrate support of 1-2 mm) of approximately +/-2.5%. However, through additional efforts, this homogeneity can be enhanced to the +/-1% best equipments values, possibly even challenging the precision of ALD (Atomic Layer Deposition) at +/-0.5%.
Beyond thickness uniformity, Sybilla equipment showcases comparable precision in chemical composition homogeneity, achieving levels as low as +/-0.5% for various materials, including the highly challenging LiNbO3, where stoichiometry serves as a critical performance indicator. Notably, on this material, we have also measured epitaxy and functional optical properties, such as refractive indexes and optical losses, with similar homogeneity precision as thickness homogeneity.
While these achievements stand as state-of-the-art results, what sets us apart, however, is our unique capability to enhance uniformity without the need to rotate or move the substrate. This key feature enables the seamless integration of additive growth techniques in both mass transport (utilizing shadow masks) and surface reaction-limited regimes (employing beam-assisted deposition). Furthermore, our combinatorial is suported by highly precise mathematical models enabling to reproduce on full substrate the corrects identified flows showing the best performances in a uniform level.To the best of our knowledge, no other equipment offers this level of versatility and precision.